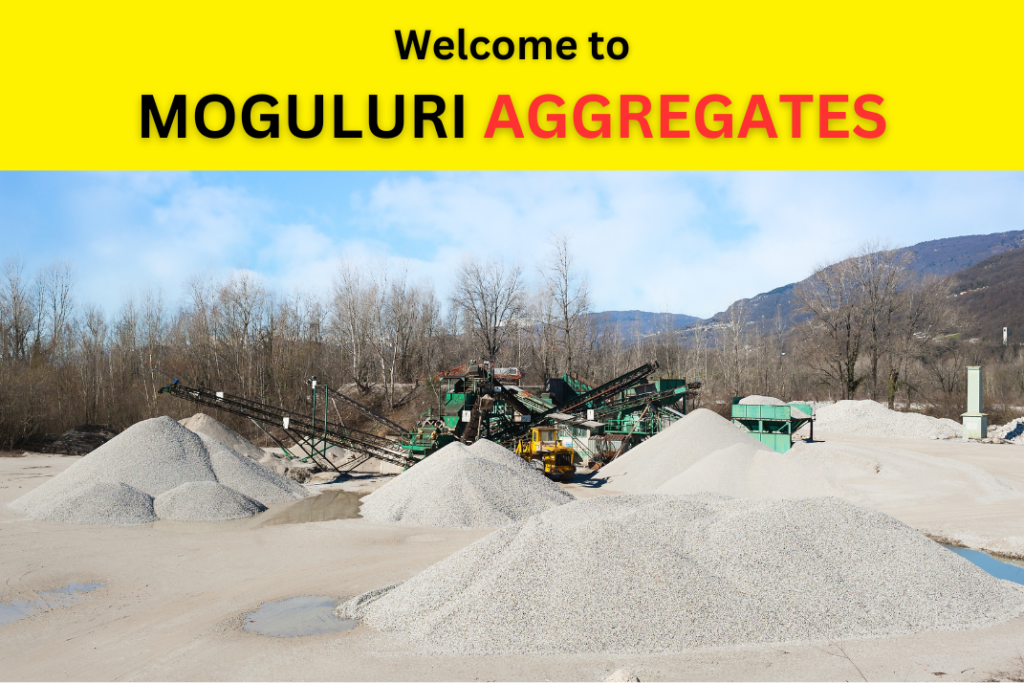
Why Choose Moguluri Aggregate Company?
- Quality Assurance:
All our aggregates meet stringent industry standards for quality and performance.
- Custom Solutions:
We offer customized orders to meet the specific requirements of your project.
- Expert Support:
Our team of experts is available to provide advice and support, ensuring you choose the right aggregates for your needs.
Moguluri Aggregate Company has been a trusted name in the construction industry, committed to providing top-notch stone aggregates that form the foundation of countless successful projects. Our dedication to quality and customer satisfaction sets us apart as a leading supplier in the region.
Explore our product range, learn more about our services, and discover how Moguluri Aggregate Company can help you build the future.
experience makes us confident
20 Years of Experience
Moguluri Aggregate Company has been a trusted name in the construction industry, committed to providing top-notch stone aggregates that form the foundation of countless successful projects. Our dedication to quality and customer satisfaction sets us apart as a leading supplier in the region.
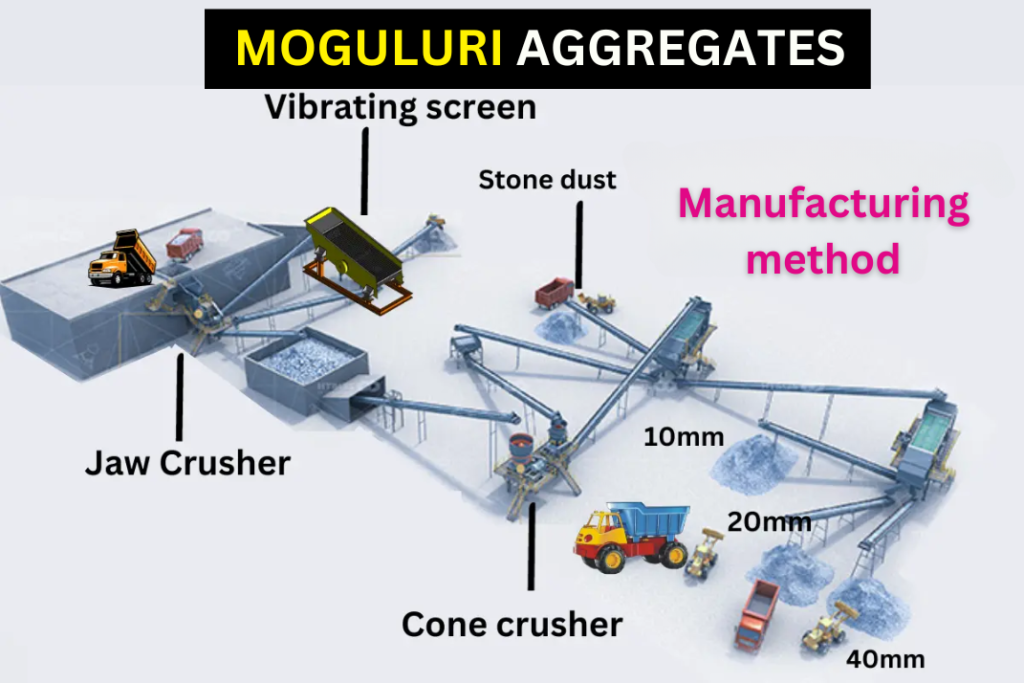
Step-by-Step Aggregate Manufacturing Process
1. Extraction
- Sourcing Raw Material: The process begins with the extraction of raw material from our carefully selected quarry sites. High-quality rock deposits are identified and extracted using controlled blasting techniques to ensure the safety and stability of the surrounding environment.
2. Transportation
- Moving Raw Materials: The extracted raw materials are then transported to our processing plant. Specialized heavy-duty trucks and conveyor systems are used to move the raw materials efficiently and safely.
3. Crushing
- Primary Crushing: The raw materials are fed into a primary crusher, which reduces the size of the large rocks into smaller, more manageable pieces.
- Secondary Crushing: The crushed material is then passed through secondary crushers to achieve the desired size and consistency. This stage ensures that the aggregates meet specific grading requirements.
4. Screening
- Separation by Size: The crushed aggregates are screened through multiple layers of vibrating screens. This process separates the materials into different sizes, ranging from fine sand to larger coarse aggregates.
- Quality Control: Regular sampling and testing are performed to ensure that the aggregates meet the required specifications and standards.
5. Washing
- Removing Impurities: The screened aggregates are washed to remove any impurities such as clay, silt, and dust. This enhances the quality of the final product and ensures its suitability for various construction applications.
6. Grading
- Sorting by Use: The washed aggregates are further sorted and graded according to their specific use. This includes different grades for concrete production, road construction, and other specialized applications.
7. Stockpiling
- Organized Storage: The graded aggregates are then stockpiled in designated areas at our plant. Each stockpile is carefully managed to prevent contamination and to maintain the quality of the aggregates.
8. Quality Assurance
- Rigorous Testing: Throughout the manufacturing process, rigorous quality control measures are in place. Our in-house laboratory conducts comprehensive tests to ensure that every batch of aggregates meets industry standards for strength, durability, and consistency.
9. Distribution
- Efficient Delivery: Once the aggregates pass all quality checks, they are ready for distribution. We utilize a fleet of modern transport vehicles to deliver our products to customers promptly and efficiently.